Anticipating and reducing EV battery supply disruptions
A recent study analyzes the relationship between electric vehicle battery chemistry and supply chain vulnerability for four critical minerals—lithium, cobalt, nickel, and manganese—across particular countries that are key contributors to production.
As electric vehicle (EV) battery manufacturing expands, so too does the demand for the materials that are essential to their production. Today’s EVs employ several battery technologies with different combinations of materials. Around the world, governments are developing policies to ensure that these materials are readily available and to mitigate supply chain disruption risks.
In a recent publication in Nature Communications, a team of researchers from the Department of Engineering and Public Policy at Carnegie Mellon University provides analysis of the relationship between electric vehicle battery chemistry and supply chain vulnerability for four critical minerals—lithium, cobalt, nickel, and manganese—across particular countries that are key contributors to production. The primary lithium ion battery chemistries used in EVs today are lithium iron phosphate (LFP), nickel manganese cobalt (NMC), and nickel cobalt aluminum (NCA), which each depend on varying amounts of these minerals. The authors, Anthony Cheng, Erica Fuchs, Valerie Karplus, and Jeremy Michalek, find that effectively reducing vulnerabilities to disruption related to any particular country may require addressing multiple layers of upstream supply relationships.
We need to anticipate new potential supply chain vulnerabilities so that we can act strategically to mitigate risk.
Jeremy Michalek, Professor, Mechanical Engineering and Engineering and Public Policy
“In the 1970s, several global oil supply disruptions sent shock waves through the economy, with motorists waiting in long lines to fill up,” says Michalek, a professor of engineering and public policy and mechanical engineering and who also serves as director of Carnegie Mellon’s Vehicle Electrification Group. “As we shift away from gasoline toward electric vehicles, we need to anticipate new potential supply chain vulnerabilities so that we can act strategically to mitigate risk.”
By mapping the supply chains of the four critical materials, calculating a vulnerability index, and using a network flow optimization to bound uncertainties, the study finds that production at multiple supply chain steps is highly concentrated in single countries. In particular, production at multiple stages of the supply chain across battery technologies occurs in China, primarily due to its role in materials refining and cathode production.
“Our approach provides a new measure of energy security as we move beyond fossil fuels,” says Karplus, a professor of engineering and public policy and associate director of the Wilton E. Scott Institute for Energy Innovation.
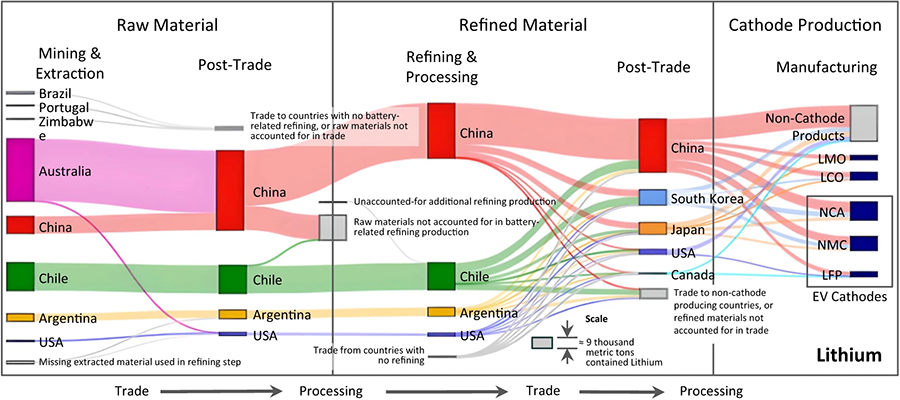
Source: Nature Communications
A Sankey diagram for global flows of lithium that available data suggest are involved in battery material supply chains.
A supply chain disruption centered in one country could occur for any number of reasons, ranging from geopolitical strategy to political or economic instability, a natural disaster, or another pandemic. Last year, China restricted exports of graphite, another key material used in batteries. Countries that make EVs, like the U.S., have an interest in diversifying supply chains to reduce disruption risks such as this.
Additionally, the research finds that the levels of vulnerability vary based on the lithium-ion battery chemistry. For example, the LFP chemistry may currently be more vulnerable to supply disruptions in China, but NMC chemistries depend on more critical materials, resulting in more pathways for disruptions from other countries to affect the supply chain, such as the Democratic Republic of Congo or South Africa.
As efforts are made to diversify the supply chain and incentivize domestic production, the authors note that a comprehensive approach must be considered beyond battery cell and pack production, including minerals extraction, processing, and component production.
“The U.S. Inflation Reduction Act provides major incentives to diversify the supply chain and build more batteries in the U.S.,” says Michalek. “We’re actively working to analyze how this policy may incentivize changes in different parts of the supply chain and in battery technology.”
The findings in this research can be useful to policymakers as they seek to identify specific bottlenecks, key relationships, and potential levers for reduction of supply chain vulnerabilities.