Mill 19 growing a digital backbone
New project advances MFI’s mission to lead the digital transformation of manufacturing by making its data readily available for advancing digital twin and AI-related manufacturing research.
At Mill 19, where the Manufacturing Futures Institute (MFI) has embarked on a mission to lead the digital transformation of manufacturing, a new project is underway. Carnegie Mellon engineers and scientists are building the foundational technology infrastructure that will support and enable data-driven advanced manufacturing research for decades to come.
Commonly known as a digital backbone, this technology infrastructure for connecting, collecting, and contextualizing research data generated throughout the facility will enable researchers to build, apply, and leverage curated and trusted data sources that will be the fundamental building block for the digital transformation of manufacturing.
This foundational infrastructure provides a platform upon which comprehensive virtual representations of equipment, processes, products, and materials can be built to mirror their physical counterparts creating digital twins—the real-time or near real-time dynamic simulations of the physical entities.
The digital backbone is essential infrastructure for MFI’s research that converges new manufacturing technologies, artificial intelligence, digital twins, and virtualized environments.
Gary Fedder, Faculty Director, Manufacturing Future Institute
“We define digital twin as a machine-readable model of a physical element that is physically realistic, capable of predictive simulation, updated through data with its physical twin’s behavior, and interoperable with its surrounding physical and virtual environment,” said Gary Fedder, MFI faculty director.
Recent investments in the wired and wireless data networks within CMU’s Mill 19 facility have expanded the digital connectedness within the building, providing pathways to virtual machines for data archival on CMU’s Campus Cloud, which provides virtual servers and associated data storage on the secure Carnegie Mellon University network.
Rod Heiple, director of the Manufacturing Futures Institute at Mill 19, noted, “Proper archival data, while necessary, is by itself insufficient. We needed a way to transform data to contextualized and useful information so that the researchers can use that information to optimize the performance of systems, machines, and processes.”
Enter the role of data historians, which are systems that collect, store, and retrieve time-series data from equipment sensors and IoT devices. Originally developed in the late 1980s, data historians are not new to CMU. The university’s Facilities Management Services (FMS) division has been using the AVEVA PI System to connect, collect, and contextualize building systems data for the university since 2015.
While many commercially available and industry accepted data historian options exist, MFI elected to build upon the university’s AVEVA PI system in order to leverage the perpetual complimentary academic software license, which is already being used successfully by FMS and is supported by the university’s Computing Services and Applications Management divisions.
In addition to implementing the AVEVA Pi system, MFI engaged Bryan Webler, professor of materials science and engineering; Sneha Prabha Narra, assistant professor of mechanical engineering; and their research teams to help define the data connection, collection, contextualization, access, analysis, and visualization requirements for the TRUMPF Tru Laser Cell 3000 and the Lincoln Electric Wire Arc Additive Manufacturing (WAAM) equipment at Mill 19.
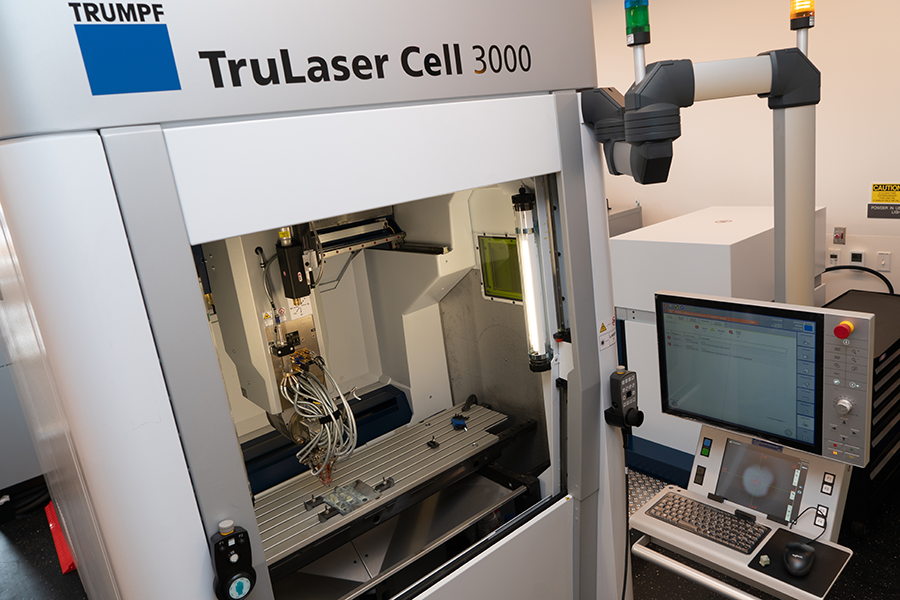
The TRUMPF TruLaser Cell 3000 will be one of two 3D printers that will be used to begin the digital backbone project at Mill 19.
Webler described the initial stage of their project as a test case which will help to determine what types of data to collect; how to organize the data; and how to motivate users, particularly student researchers, to contribute their findings.
“We use the acronym FAIR to explain that the data needs to be Findable, Accessible, Interoperable, and Reusable,” explained Webler during MFI’s recent Technical Exchange event during which he and Narra described the digital backbone and their pilot project to members of the MFI partnership program.
Most recently, MFI hired Stephanie Steren-Ruta into the role of Advanced Manufacturing Engineer – Digitalization. Steren-Ruta will work closely with Mill 19 researchers to ensure the connectedness of research projects to the data historian through the digital backbone and provide the training, processes, and procedures required for its use.
An electrical engineer by training, she led a corporate-wide effort at Bridgestone to develop, deploy, standardize, and enhance tire testing machine capabilities. Her six years at Bridgestone provided opportunities to expand her engineering software development and data management skills.
Steren-Ruta’s interest in both technology and Carnegie Mellon was sparked when, as a 10-year old, she witnessed a robotics demonstration while visiting campus with her father, who was here as a visiting professor.
“The experiences of that day captivated my younger self, sparking a lasting fascination, and from that moment forward, I was determined to make a contribution to that space,” said Steren-Ruta.
“We are extremely excited to have the digital backbone ready for operation in early 2024. It is essential infrastructure for MFI’s research that converges new manufacturing technologies, artificial intelligence, digital twins, and virtualized environments,” said Fedder.