3D printing nanoparticle neural probes
Rahul Panat has received a R01 grant from the NIH to use a low-cost, rapid additive manufacturing method to create a new class of high-density neural probes to record neurological data.
Carnegie Mellon University’s Rahul Panat and Eric Yttri have received a R01 grant of $1.95 million from the National Institutes of Health (NIH) to use a low-cost, rapid additive manufacturing method to create a new class of high-density neural probes to record neurological data.
The grant, which is part of the federal Brain Research through Advancing Innovative Neurotechnologies (BRAIN) Initiative, supports research that will create an entirely new manufacturing method for the fabrication of neural probes based on 3D nanoparticle printing. This new technology will dramatically increase accessibility to brain tissue, as well as the number of electrodes that can fit in a small area, and will give researchers the ability to prototype new electrode configurations at the click of a button, on-demand, within a few hours.
“This research proposes to use a novel additive manufacturing (AM) method that uses 3D nanoparticle printing to fabricate customizable, ultra-high density neural probes, such as brain-machine interfaces or BMIs,” says Panat, an associate professor of mechanical engineering and a member of Carnegie Mellon’s Next Manufacturing Center. “The recording densities of the probes will be an order of magnitude higher than that made by any current method.”
Many existing 2D and 3D arrays of silicon electrodes are prohibitively fragile and expensive, and thus they are impractical for use in many contexts. Additionally, these existing arrays have a relatively low density of electrodes, meaning that they cannot achieve the resolution required for applications such as precision neuroprosthetics.
However, Panat and Yttri’s new 3D nanoparticle printing technology promises to overcome the field’s current limitations in terms of sampling, structure, reliability, and cost. By producing customizable, 3D printed neural probes, the team believes that their research has the potential to profoundly change the course of neuroscience research.
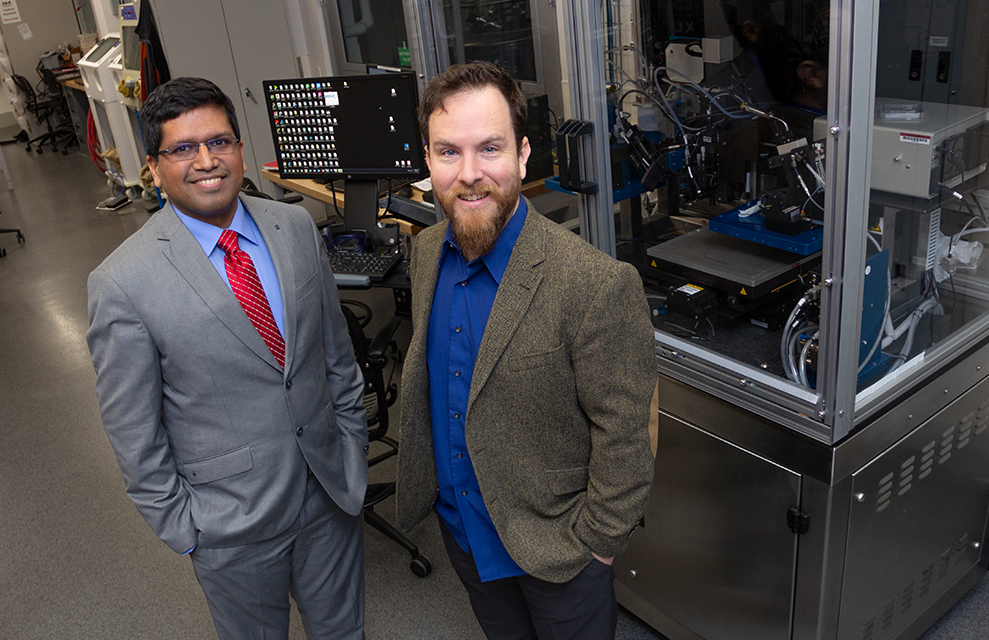
Source: College of Engineering
Rahul Panat, an associate professor of mechanical engineering and a member of Carnegie Mellon’s Next Manufacturing Center, with Erik Yttri, an assistant professor of biological sciences.
“With fMRI we can see the whole brain, but the temporal and spatial resolution are not where we need them to be. Electrodes can give us millisecond, single neuron resolution, but even with the most recent advances you might only be able to get information from 300 or 400 neurons at a time,” adds Yttri, an assistant professor of biological sciences. “With my expertise in neuroscience and Rahul’s pioneering 3D printing technique based on aerosol jet technology, we decided to combine our interests to bridge this gap that exists between the two ways neuroscience is classically done.”
By combining their research areas, Panat and Yttri will use their unique collaboration to make an entirely 3D printed microelectrode array, the first of its kind. By using 3D printing to manufacture the arrays, Panat and Yttri will achieve a degree of customizability that is unheard of.
“If you want an electrode, typically you go to a supplier who offers 10 options, and you have to make one of those options work for any experiment,” explains Yttri. “By 3D printing the electrodes with our high throughput method, we can put the recording sites as close together or far away as we want. And the nature of the electrodes’ structure means they can be implanted in the brain much easier and with less damage than the current state of the art.”
The long-term goal for this project is to create precision medical devices, such as brain-machine interfaces (BMIs). Not only will these devices be more precise, but they will be more customizable to the patients. A patient needing an electrode for a neuroprosthetic, for example, could be given a device that, using structural MRI, could be customized on a patient-by-patient basis to map to the individual curves of the brain.
We are applying the newest advances in microelectronics manufacturing to neuroscience in order to realize the next generation tools for the exploration of the brain.
Rahul Panat, Associate Professor, Mechanical Engineering
“We are applying the newest advances in microelectronics manufacturing to neuroscience in order to realize the next generation of tools for the exploration of the brain,” says Panat. “This research will lead to a more precise 3D mapping of neural circuits and precision neuroprosthetic devices that can restore significantly more of patients’ previously lost functionality. The research will also lead to new avenues for the treatment of neurodegenerative diseases such as paraplegia and epilepsy.”
In March 2018, the project received preliminary seed funding from an innovative grant program for cross-disciplinary foundational science research in the life sciences, called the DSF Block Grant program. Panat and Yttri are members of Carnegie Mellon’s new Neuroscience Institute.