Carnegie Mellon is a driving force to bring robotic systems into our everyday lives by building robots and robotic systems to improve performance in our work, play, and health.
Robots in the future will no longer be defined as heavy machines. Tomorrow’s robots will be smaller and designed for everyday purposes, with electronics nested into soft, technologically advanced materials.
The next generation of materials needs more than integrated sensors and actuators. They need to be highly integrated, complex, and symbiotic systems that are safe, soft, intelligent, interactive, and adaptive.
Environmentally friendly
Our AI powered robots mimic natural organisms and do not disturb sea life. They operate without motors and move and sense silently, without creating noise or acoustic traces to interfere with the environment.
Medical tracking
Tracking the body’s motion can assess changes and monitor mobility after surgery. Soft as the skin it’s on, and technically strong, this wearable systems classifies activity and range of motion to assess recovery progress and improve the patient’s physical therapy plan.
Electronic tattoos
Stretchable, inexpensive, tattoo-like circuits are made with an inkjet printer. Carnegie Mellon researchers have developed a simple, efficient method to make robust, highly flexible, tattoo-like circuits for use in wearable computing. The low-cost process adds trace amounts of an electrically-conductive, liquid metal alloy to tattoo paper that adheres to human skin. These ultrathin tattoos can be applied easily with water, the same way one would apply a child’s decorative tattoo with a damp sponge.
Exoform
Exoform, a customizable, semi-rigid material with self-fusing edges has the potential to eliminate many of the doctors visits that go along with broken bones, not to mention help them heal faster. The Exoform cast distinguishes itself from the orthopedic materials currently available at local pharmacies, such as finger splints and wristbands, in that it can successfully support a variety of complex body parts and adjust its stiffness throughout the healing process. It is also breathable and can be submerged in water, allowing for a more comfortable wearing experience.
Student research
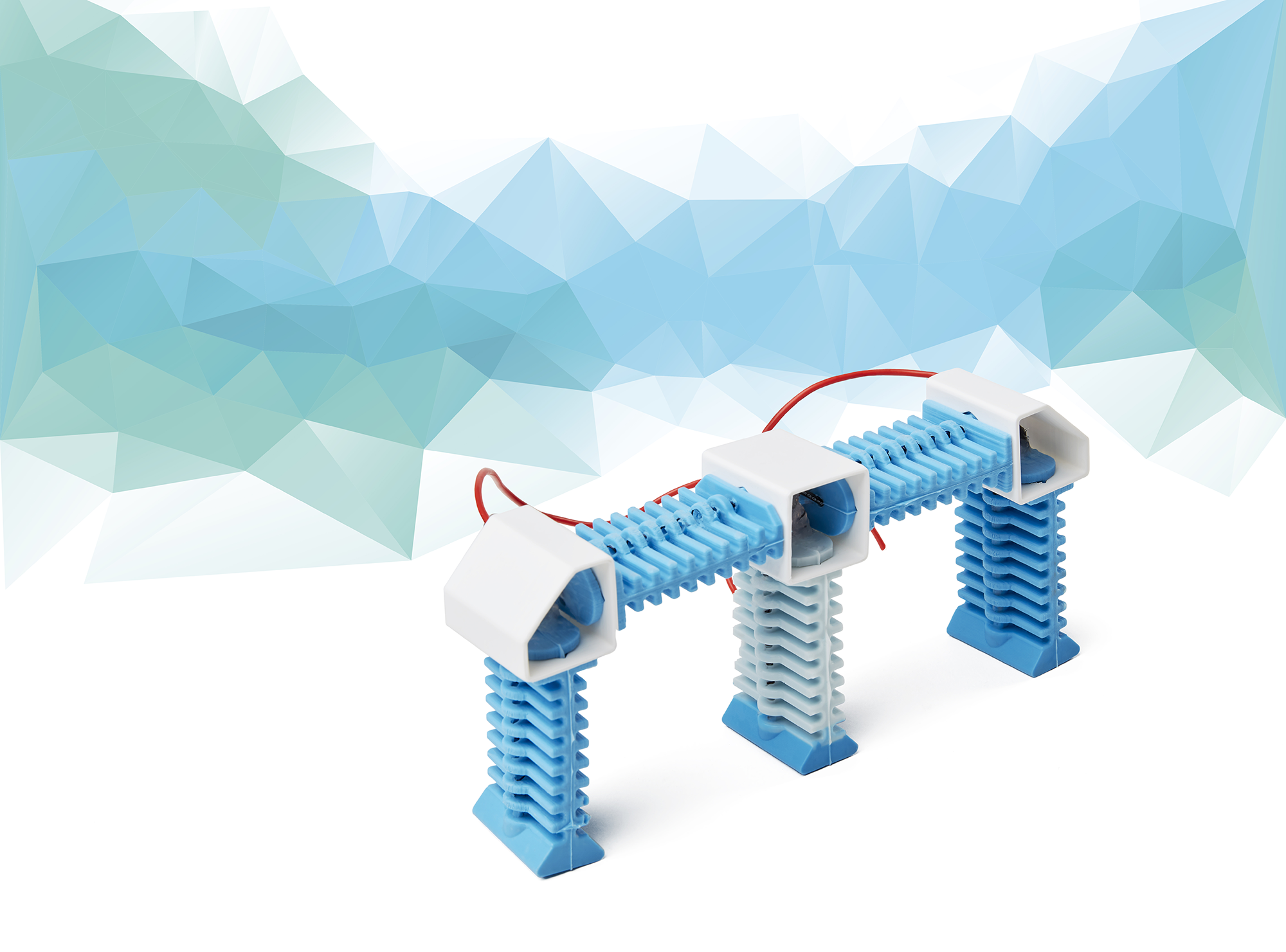
Horton, the three-limbed soft robot
Meet “Horton,” a soft robot composed of three limbs that are connected by two torso elements. Each of these five elements is composed of a soft silicone rubber that is embedded with a “muscle wire” that contracts when heated with electrical current. A nickel-titanium alloy is used as the muscle wire since it exhibits an electrically-responsive shape memory property. The soft robot is used to test out various algorithms and methods for robot locomotion and control.
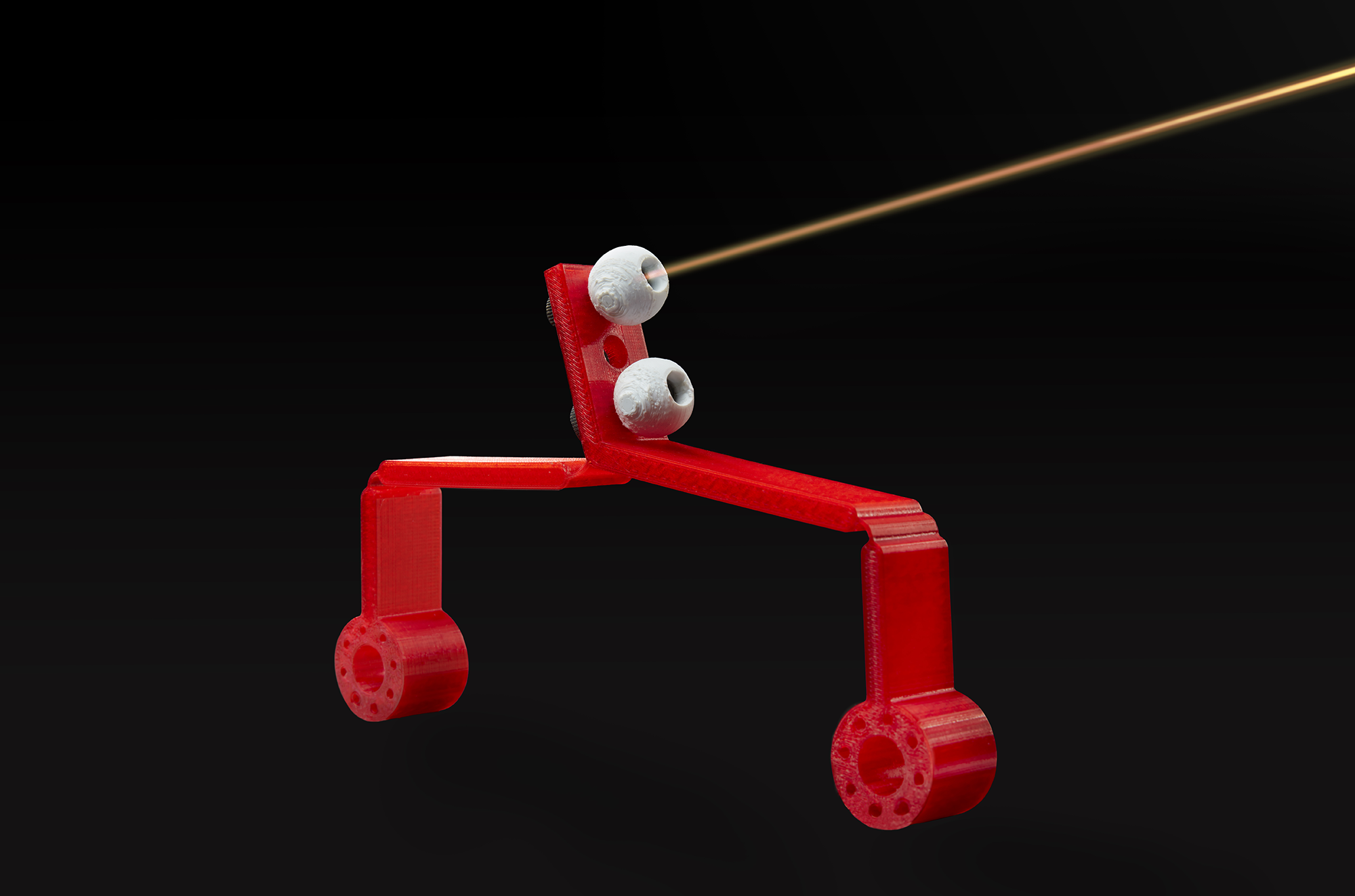
5-bar linkage with soft materials
The “5-bar linkage,” shown here, is a standard mechanism in mechanical and robotic systems. It is used to connect an electrical motor with a robot limb or manipulator for achieving robotic motion. The structure here is used to test out the long-term behavior of using soft and flexible materials in a 5-bar linkage. A camera or optical detector tracks the motion of the white ball at the top of the linkage in order to determine how the motion might change over the time after repeated cycles of operation.