Now printing: seaweed-based, biodegradable actuators
We are one step closer to naturally compostable robots now that researchers at Carnegie Mellon can print actuators using a bio-ink made from seaweed.
Traditionally, soft robots have been made using synthetic polymers, rubbers, and plastics. Such materials provide soft robots with long operational lives and stable structures, but may pose risks to the environment if lost or damaged during use. Researchers seek to minimize this risk by creating new ways to build naturally decomposable robots.
An interdisciplinary team at Carnegie Mellon University, led by faculty members Victoria Webster-Wood and Adam Feinberg in collaboration with Carmel Majidi and Lining Yao, is developing new ways to fabricate biodegradable actuators for marine applications. Using a bio-ink made of materials sourced from common brown seaweeds, the research team identified designs and printing parameters that allow water-tight structure to be printed using the FRESH Printing method.
“We are very excited to expand the fabrication capability of the FRESH Printing method and optimize it for soft robotic applications,” explained Wenhuan Sun, a recent Ph.D. student in mechanical engineering. “The unique benefits of FRESH make it possible to create robotic structures with a combination of unusual properties.”
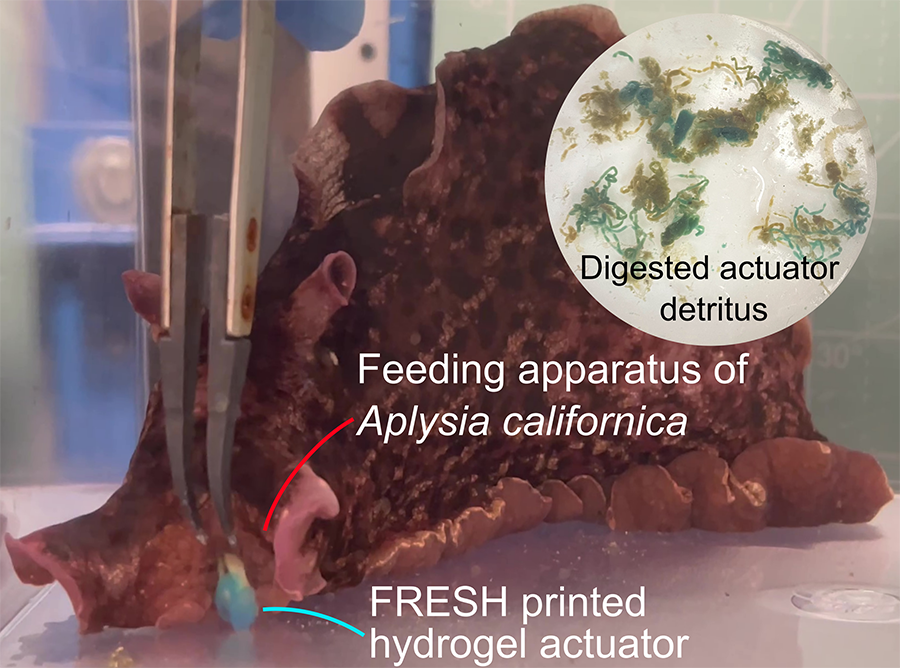
Source: Biohybrid and Organic Robotics Group
The 3D printed alginate actuators in this work are not only biodegradable, but are also safely edible and digestible by marine organisms.
Their approach, recently published in Advanced Functional Materials, allows small scale, very soft actuators that can extend, bend, and twist to be fabricated. They can also be combined into structures for gripping and positioning. The seaweed-based inks used by the research team rely on calcium to crosslink and form gels. This allowed the researchers to leverage the material properties in order to create actuators that can change shape and stiffness by varying the degree of crosslinking in the actuators.
“How do we balance the need for advanced soft robotic structures with the potential environmental impact that results from their creation? We believe that the biodegradable actuators printed using FRESH are a promising solution, and we are excited to continue making improvements,” said Ravesh Sukhnandan, a Ph.D. student in mechanical engineering.
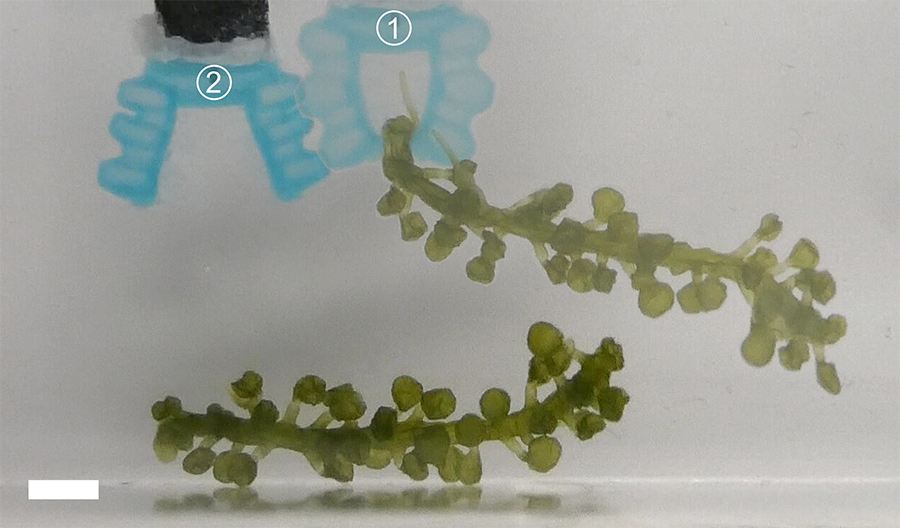
Source: Biohybrid and Organic Robotics Group
A 3D printed alginate gripper safely handles and moves a fragile piece of seaweed.
The actuators’ capabilities don’t stop there. In addition to their robotic functionality, the actuators are fully biodegradable, degrading in natural ocean conditions within seven days. The actuators can also be safely consumed by marine organisms. This means that if lost or damaged during use, the actuators pose minimal risk to the environment.
Wenhuan Sun graduated in the fall of 2023, but he has stayed in touch with the research team to help onboard and train the next generation of biodegradable robotics researchers. MS-BRIDGE Fellow Avery Williamson and GEM University Fellow Ravesh Sukhnandan have continued to develop the technology under the guidance of Webster-Wood, Feinberg, Majidi, and Yao. They hope to further understand actuator performance in natural environments and extend this printing approach to complete robotic structures.
How do we balance the need for advanced soft robotic structures with the potential environmental impact that results from their creation? We believe that these FRESH printed biodegradable actuators are a promising solution.
Ravesh Sukhnandan, Ph.D. student, Mechanical Engineering
“We are thrilled to be able to continue this project where Wen left off,” said Williamson. “It’s incredibly exciting to be developing new tools and methods for technologies with clear sustainable applications.”
Victoria Webster-Wood is an associate professor of mechanical engineering. Adam Feinberg is a professor of biomedical engineering and materials science and engineering. Carmel Majidi is a professor of mechanical engineering. Lining Yao is an assistant professor of human-computer interaction.