A crystal-clear way to save time
Chemical engineering researchers developed a new way to process diblock polymer materials that significantly reduces production time.
Chemical Engineering researchers recently discovered a better way to make a new class of soft materials—reducing a process that used to take five months down to three minutes.
Connor Valentine, a chemical engineering Ph.D. student, and Lynn Walker, professor of chemical engineering, work with diblock polymers. Diblock polymers are chain-like molecules where one end of the chain is hydrophobic, and the other is hydrophilic. Molecules like this are used in soap because the hydrophobic side grabs onto dirt and oil, but the hydrophilic side keeps the molecules dissolved into the water.
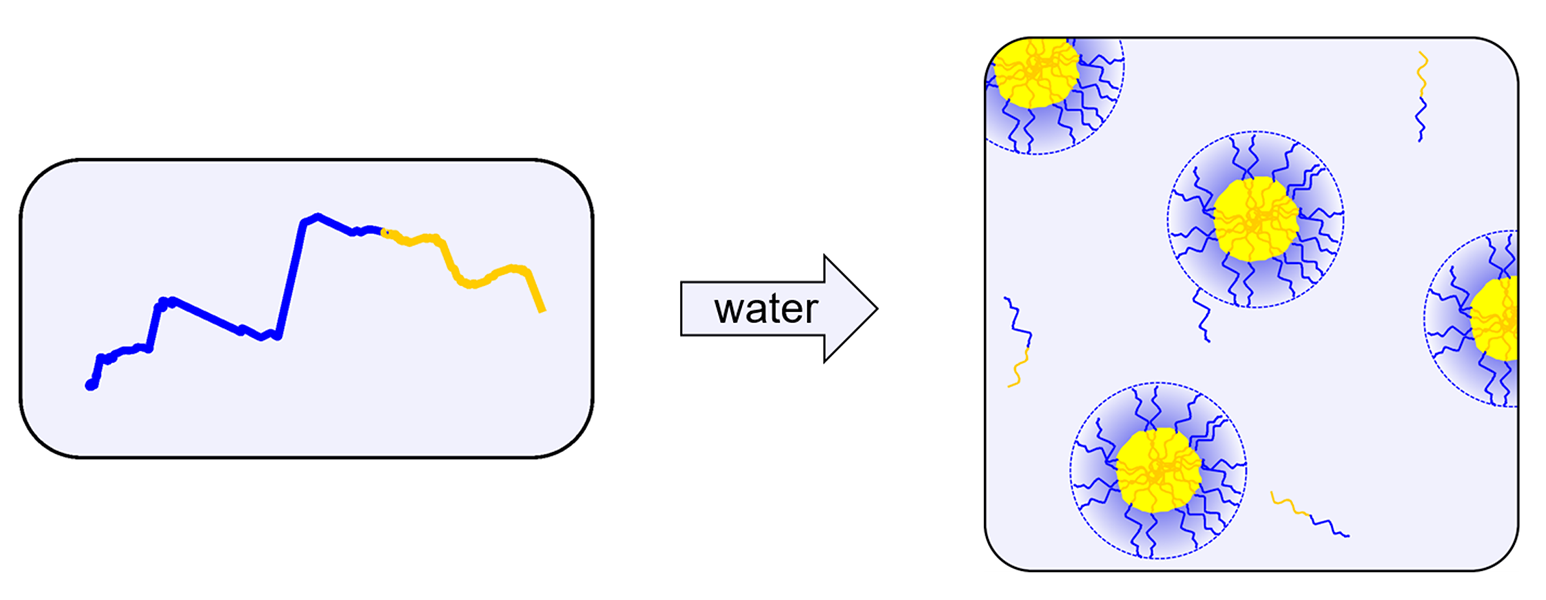
Source: Connor Valentine
The blue end of each chain is soluble in water, while the yellow end is not. The yellow ends aggregate together in an effort to separate from the water. These ball-shaped clusters are called micelles.
When these molecules are placed in water at high enough concentrations, they begin to form clusters: the hydrophilic parts clump together in the center of the ball in order to avoid water. The hydrophobic sides arrange into a brush-like layer on the outside of the ball, protecting the hydrophobic center.
As you add more polymers into the water, however, they begin to run out of room and stack themselves intelligently and spontaneously. It would be as if you were trying to fit the maximum number of tennis balls in a box—you would carefully stack each layer.
When they form these stacks, they are called crystals, because the organizational patterns will repeat over and over in every direction. Crystalline structures like this are found throughout nature, including in gemstones, metals, and polymeric materials. People have taken advantage of the repeating and consistent spacing to create polymeric membranes for filtering water and gases. There are also exciting potential uses in new soft materials, with applications that include medical implants, adhesives, sustainable food packaging, liquid beauty products, and even condiments.
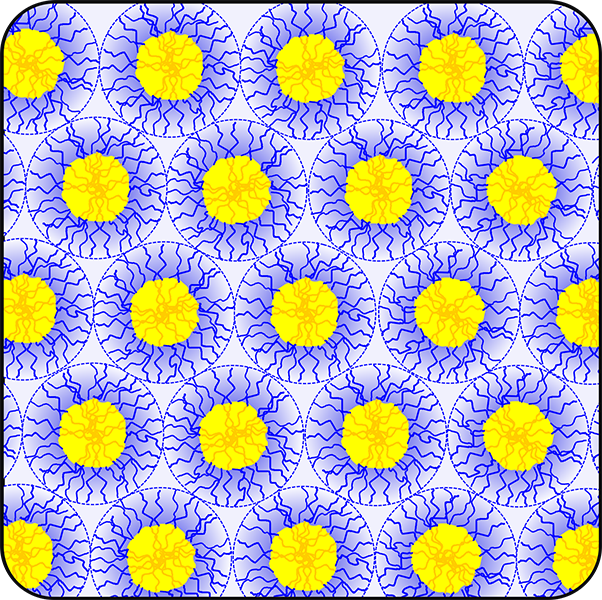
Source: Connor Valentine
The polymer aggregates form spheres, which pack tightly into layers at high concentrations. Around 40% by weight of this sample is water.
However, the problem comes in when researchers are trying to make specific crystalline structures. Engineers need to be able to consistently produce crystals with specific arrangements and sizes so that they can achieve the desired material performance at market scale. However, processing issues can arise when they don’t fully understand the forces driving crystal formation. The wrong temperature change, mixing speed, or formulation can cause crystals to suddenly form, degrade, or transition to another crystalline organization. The accompanying change in material properties can jam mixers, ruin equipment, and result in a worthless final product.
In the case of this work, the desired crystalline state can take months to form at room temperature. This can cause huge issues, with companies discovering they have a product with completely different properties after three months—maybe it’s chunky, or it’s become stiff—or perhaps the company just has to wait three months to sell their product because it takes that long to get the gel consistency they desire.
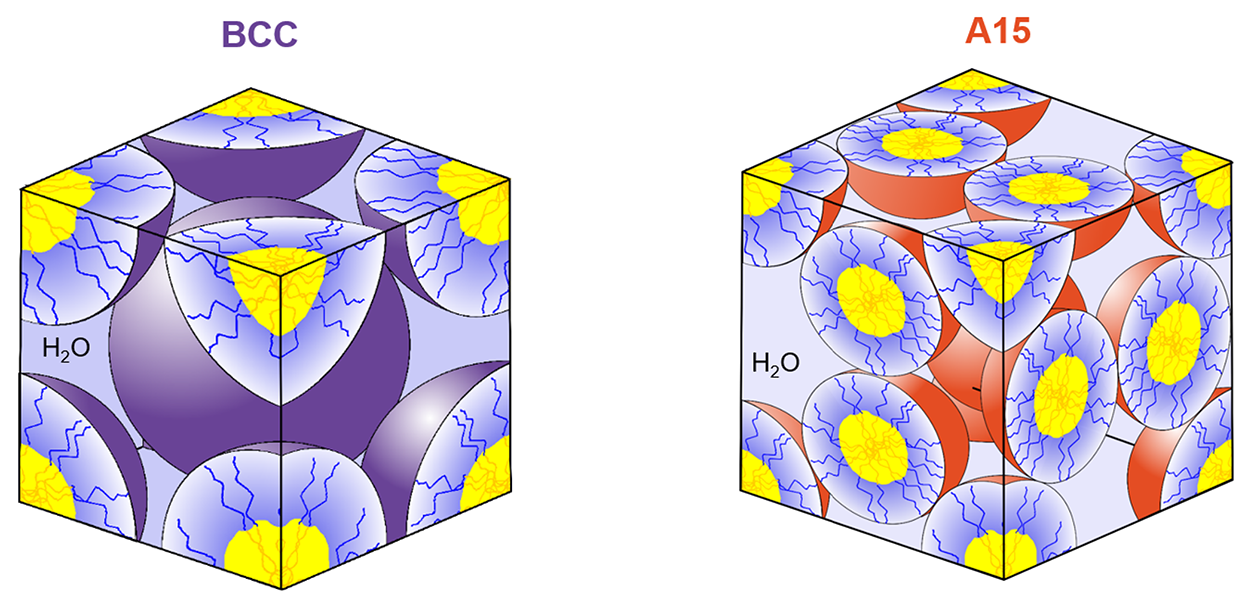
Source: Connor Valentine
Two crystalline phases found in the diblock polymer materials used in this work. With the proper thermal and shear processing, these “unit cells” can repeat hundreds of thousands of times in every direction in perfect symmetry.
“It’s important for people to understand how these polymer molecules will turn into crystals,” says Valentine. “And that’s not just if they turn into the crystal they want, it’s the rate of it, the speed. Also, are there going to be other crystal phases present? Is every piece of that crystalline material going to be oriented consistently?”
Valentine and Walker worked with collaborators from the University of Minnesota, who discovered that the rate of heating and cooling can produce intermediate crystal structures that last for several months. Valentine’s team built on the work of their collaborators and investigated the impact of shear processing on these crystal structures. Shear processing is a broad term that includes steps like mixing, painting, coating, and shaking—the material is moving. The speed, duration, and direction of shear can really matter for materials like those used in this work.
“Ketchup is a great example about why shear processing affects soft materials because ketchup has a yield stress and thins when you mix or process it,” explains Valentine. “If you’re trying to get ketchup out of a glass bottle and it is gel or solid-like, it will not flow. But small taps (on the correct part of the bottle) will get the ketchup to flow very nicely. The shear is changing the microstructure of the ketchup, which then changes the flow properties. It’s important we understand how shear impacts any material we work with in the same way.”
In this work, the authors used an oscillatory shear flow, which involves placing the gel or soft material between two parallel plates—where the top plate can rotate back and forth. Researchers can control the speed and length of the top plate. When Valentine and his team put the diblock polymer crystals into this shear cell, they were able to cause the crystalline phase to change into the equilibrium structure within three minutes. The Minnesota team had previously found this same structural change to take almost five months sitting at room temperature without shear.
“Shear processing can help with the dynamics, the speed, and the rates of structural change, not just the final result, which is something people don’t really think about,” says Valentine. “They often think when you shear these materials, it’s going to change the structure into something different, but that’s not necessarily true.”
The team was able to measure these results by visiting the Advanced Photon Source Synchrotron accelerator at Argonne National Laboratory, which is essentially a mile-wide particle accelerator. Electrons are accelerated around the circle of the facility at almost the speed of light, and every time they turn, an x-ray beam leaves the circle. They used these high-intensity x-ray beams to measure the crystal structure in real-time.
Their findings, published in ACS Macro Letters, not only showed that the speed increase occurs, but also detailed how to tune the shear parameters to achieve the desired rate of crystal formation. They even found that you can prevent the change from happening entirely if the shear is at very low frequencies with very long cycles of oscillation.
“We were able to show that this shear processing step is just a very controllable way to get the structure you want and how fast you want it,” says Valentine.
The research was done in collaboration with Ashish Jayaraman and Mahesh K. Mahanthappa, both of the University of Minnesota.
Photo at top by Argonne National Laboratory shows Advanced Photon Source Synchrotron accelerator, a mile-wide particle accelerator.