Tuning synthetic collagen threads for biohybrid robots
Researchers in Victoria Webster-Wood’s Biohybrid and Organic Robotics Group are using techniques from tissue engineering to refine tendon-like collagen threads for a new generation of robots.
The idea of incorporating actual muscles or neurons into a robotic system might sound like some sort of science fiction, but researchers in Carnegie Mellon’s Mechanical Engineering (MechE) Department are taking steps to make it a reality.
This field, known as “biohybrid robotics,” is the central focus of the Biohybrid and Organic Robotics Group (B.O.R.G.), led by Victoria Webster-Wood, an assistant professor of mechanical engineering.
“Our ultimate goal is to be able to use biological materials as engineering materials in robotics to create renewable, biodegradable robots,” she says.
Our ultimate goal is to be able to use biological materials as engineering materials in robotics to create renewable, biodegradable robots.
Victoria Webster-Wood, Assistant Professor, Mechanical Engineering
In a recent paper published in The Journal of Biomedical Engineering, MechE Ph.D. student Wenhuan Sun aimed to better understand how to fabricate material threads to use in these special robots. The threads are made from collagen, a naturally-occurring protein found in structural tissues like skin, ligaments, and tendons.
In essence, the goal of this research was to better understand how to make an artificial tendon for use on a robot. In our bodies, tendons work to connect muscle to bone and are rather strong. This means that these collagen threads could be used for a very similar purpose in a robot, connecting living muscle actuators to the robot, helping it to walk, jump, or swim.
But the mechanical properties of the robot’s materials can have a big effect on how living muscle actuators grow and perform.
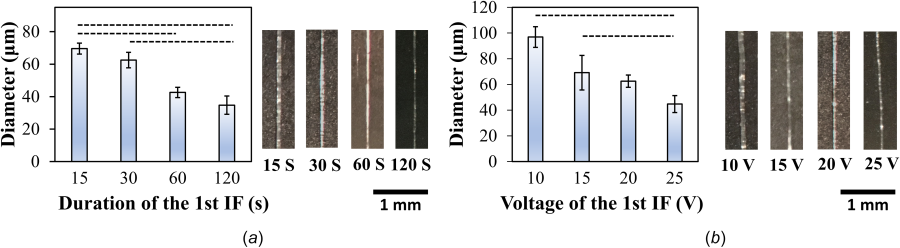
Source: College of Engineering
Different parameters like duration times and voltages lead to different-sized threads, pictured here. Despite their relative strength, the threads are incredibly thin.
This means that Sun would not only have to understand how best to create these collagen threads, but also explore how to tune their mechanical properties. Depending on what you want your robot to do, you might need a material that’s more muscle-like or more tendon-like.
Sun’s threads were created using a technique called “electrocompaction.” It was first developed for use in tissue engineering, and is now being fine-tuned by groups like the B.O.R.G.
To create the threads, collagen fibers are moved through a special type of cell called an “electrocompaction cell” thanks to the charge that they naturally carry. The fibers will eventually get compacted together in the process, creating electrochemically aligned collagen (ELAC) threads.
Sun wanted to investigate just how much you could tune this compaction process to create different threads, in order to diversify the fabrication process as a whole. Previous work from tissue engineering primarily focused on making the strongest, most tendon-like threads possible. Biohybrid robotics require a bit more nuance and finesse.
When first compacted, however, the threads are surprisingly brittle and hard to work with—not yet robust like natural tendons. Sun recounted the difficulty of just trying to place the compacted threads in a plastic container. “Because there’s static around the plastic container, the thread wants to cling or stick to either side of the walls. That would make things very difficult,” he explained.
Even though the threads can be rather long—Sun mentioned creating one that was up to 40 centimeters (around 15 inches)—they’re incredibly thin. The widths ranged from approximately 50 to 100 microns—far less than the smallest measurement on any ruler.
But, with some time and practice, he was able to carry out a series of experiments determining how a set of fabrication parameters affect the resulting thread. He also studied the interactions between these parameters and was able to achieve a wide range of tunable properties.
Even though their results were somewhat expected—more time spent allowing the threads to compact led to stronger, larger threads, for example—this study was the first, verifiable evidence of their suppositions and will help future researchers design and select electrocompacted collagen materials for their own work. Sun was even able to train a deep neural network in order to recommend specific fabrication parameters based on what mechanical properties a particular researcher might want.
So now that we better understand how to make these threads, what can we actually do with them?
The possible answers to this question are nearly endless, but for Sun, he aims to feed the threads into a 3D printer so they can be used to create different shapes and structures. He’s currently working alongside Adam Feinberg, professor of biomedical engineering and materials science and engineering, to do exactly that. The strength of the compacted collagen threads means that they could be used for a broader set of applications than soft, squishy, muscle-based prints, and likely will help a new generation of biohybrid robots get off the ground, quite literally.
This paper was published in May 2021 in The Journal of Biomedical Engineering. Other authors include biomedical engineering master’s student Jason Paulovich, who is now pursuing a Ph.D. in biomedical engineering at South Dakota School of Mines and Technology.