Robotic innovation to transform U.S. manufacturing
As Carnegie Mellon celebrates another milestone in the construction of the Robotics Innovation Center, its Hazelwood Green neighbors at Mill 19 are leading manufacturing robot research for the nation.
Among the large and enthusiastic crowd who gathered at Hazelwood Green to celebrate the completion of the steel frame of Carnegie Mellon’s Robotic Innovation Center (RIC) was Gary Fedder, the faculty director of the Manufacturing Futures Institute (MFI), who will be a neighbor, ally, and valued partner in the robotics education and research that will be conducted at the 150,000-square-foot facility when it opens in 2025.
Fedder, also a professor of electrical and computer engineering, is leading the advancement of robotic applications for manufacturing and oversees the increasing investments being made by the federal government in robotics for manufacturing programs at Carnegie Mellon.
“Our mission at MFI is to catalyze research and education in advanced manufacturing for the benefit of the country,” said Fedder.
Our mission at MFI is to catalyze research and education in advanced manufacturing for the benefit of the country.
Gary Fedder, Faculty Director, Manufacturing Futures Institute
Fedder was one of the first to take up residence at Hazelwood Green where MFI shares space at Mill 19 with the Advanced Robotics for Manufacturing Institute (ARM) and Catalyst Connection, which provides consulting and training services to small and medium-sized enterprises (SMEs) in southwestern Pennsylvania.
ARM is working with Carnegie Mellon engineers and scientists to accelerate the adoption of robotic technology for industry. They are collaborating on several federally-funded projects.
In 2022, the ARM Institute received a $14.2 million Build Back Better Regional Challenge (BBBRC) grant, which they are using to help SMEs de-risk off-the-shelf technology that can be integrated into manufacturer’s production lines. Catalyst Connection leads a complementary BBBRC project, with MFI providing supporting expertise, to assist regional SMEs with adoption of robotics and digitalization technologies to help their businesses stay competitive.
The National Institute of Standards (NIST) is funding another project, led by MFI and including ARM, to establish a Robotics Training Center for U.S. manufacturing. The multi-thrust project aims to develop and deploy machine learning techniques that can rapidly train robots to perform manufacturing tasks.
And in March of this year, another federal award from the Department of Defense established the AI Data Foundry (AIDF), a new project being led by ARM in partnership with Carnegie Mellon and Catalyst Connection to develop a national center that will collect and aggregate data for robots working in manufacturing settings. Carnegie Mellon will develop the machine learning algorithms and toolboxes manufacturers need to advance robotic technology within the AIDF.
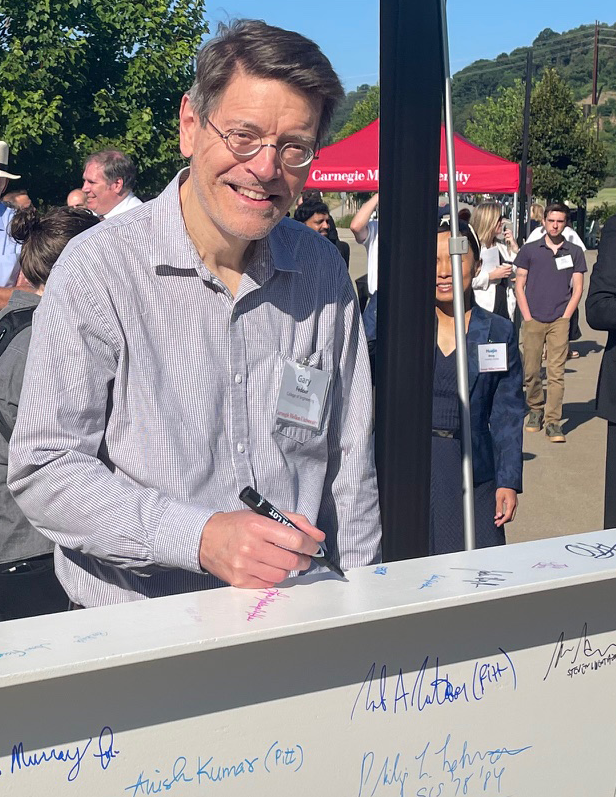
Gary Fedder, the faculty director of Carnegie Mellon’s Manufacturing Futures Institute, adds his name to the final steel beam at the topping off ceremony for the Robotics Innovation Center.
Learning lab resources are also being developed that will be installed throughout the Mill 19 facility to promote advanced manufacturing and educate high school students, manufacturing workers, and industry leaders.
Fedder and his MFI colleagues have a vision for how robot capabilities will evolve and what it will take for them to attain the skills needed to empower a new level of automation and productivity throughout the U.S. manufacturing sector.
Common use cases in manufacturing include insertion tasks such as plugging cables into sockets, inserting pegs into holes, and screwing nuts and bolts together. While these are all easy for humans, they are challenging for robots, particularly in applications where the parts are not uniformly presented to the robot. And robots have difficulty recovering when something goes wrong.
“We know we can train robots to perform repetitive, predictable tasks, but now we must make even smarter robots—robots that can recover from errors, adapt to real-time circumstances, and reconfigure what they do based on changing real-world scenarios,” explained Fedder.
However, AI and machine learning approaches used in manufacturing systems need training and validation from curated data resources, often coupled with new sensing and control methods to generate useful data and subsequently act. Carnegie Mellon and ARM engineers and scientists are developing pretrained models that manufacturers will eventually be able to use to quickly and easily customize for their specific manufacturing tasks.
Perhaps most exciting is the potential that digital twins have to advance manufacturing systems. A digital twin serves as a living predictive model and its surrounding manufacturing environment (i.e., the physical twin) and operates in a bi-directional manner. That means live data is continually updating the model so that the computing system is aware of the most current information and can understand both the robot and the physical environment in which it is operating and then execute or recommend appropriate actions. Digital twin technology enables real-time monitoring and predictive maintenance, and, in the future, it will enable co-optimized efficiencies with other digital and physical assets throughout the manufacturing ecosystem.
Fedder is confident that Carnegie Mellon is ideally suited to lead these efforts.
Not only is Carnegie Mellon a pioneer in computer and AI technology and a leader in engineering and manufacturing research and education, but the culture of the entire university is extraordinarily collaborative and creative, which attracts engineers and scientists who want to work together to solve these big challenges.
Gary Fedder, Faculty Director, Manufacturing Futures Institute
“Not only is Carnegie Mellon a pioneer in computer and AI technology and a leader in engineering and manufacturing research and education, but the culture of the entire university is extraordinarily collaborative and creative, which attracts engineers and scientists who want to work together to solve these big challenges,” said Fedder.
Pictured, top: Multiple manufacturing robots in the high bay at Mill 19 are being used by MFI and the ARM Institute to de-risk robot applications for manufacturers.