Predicting portable power
Researchers at CMU and the University of Texas at Austin have designed a model that accurately predicts a battery’s charge curve, which could impact the safety and reliability of electric vehicles.
Lithium ion batteries are the go-to power source for many of our favorite devices like cell phones and laptops, and their presence will continue to expand as electric vehicles become the new standard, replacing gasoline-powered cars.
Using a portable power source requires top-notch safety and maintenance features. A team of researchers from Carnegie Mellon University and the University of Texas at Austin has designed a battery management system to run crucial diagnostics on battery health so that drivers are able to make informed decisions. The model looks at two key diagnostics, the state of charge and state of health. In the short term, looking at the state of charge lets drivers know if they have enough power to reach their destinations, while in the long-term, battery health data can determine whether it’s time to replace a battery based on its ability to hold a charge relative to when it was new.
Reeja Jayan explains that while battery management systems already exist in most electric vehicles, there are a few qualities that make this new model stand out from the rest.
“We had a database of around 11,000 experimentally collected charging curves for a particular battery cathode chemistry,” said Jayan, an associate professor of mechanical engineering. “We used them to train a machine learning model to predict complete charging curves using sparse data inputs.”
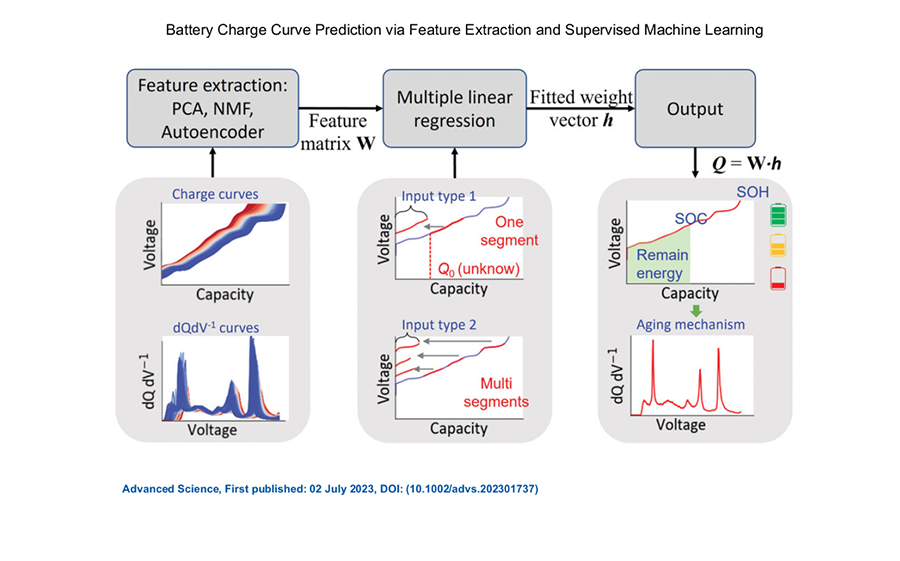
Source: Advanced Science
A look at how the machine learning model predicts a battery’s charge curve in the short term and assesses its long-term charging capacity relative to when the battery was new.
What’s unique and practical about this research is that this machine learning based battery management system takes minimal data—just five percent of a battery’s charge curve—and produces a charging prediction whose margin of error is two percent. Data collection itself is much simpler, too, requiring only about 15 minutes of charge time to calculate the curve and determine battery health. This information can even be collected in increments, so even if charging were interrupted, it would not ruin the analysis that was in progress. With such an impressive accuracy rate, this model was used to make predictions on an entirely different cathode chemistry. An updated version will be less data-driven and instead incorporate physics components into a calculation of a battery’s charge curves. While the laboratory-collected datasets were useful for training the original machine learning model to make predictions, this source also had limitations because it didn’t help researchers pinpoint the specific factors that cause batteries to fail.
“The charge curves we used in the study were collected at a constant c-rate and at room temperature,” Jayan said, “but charge current and temperature vary a lot in real-world battery applications. Collecting and using real data as input for the machine learning models will be an important next step to improve the model.”
Using environmental factors to calculate a battery’s charge and eventually discharge curves would go beyond a level of complexity that humans could produce.
Neural network models take things a step further by learning why there might be a dip in a battery’s charging capacity—if a particle breaks, for example.
Reeja Jayan, Associate Professor, Mechanical Engineering
“Right now we have a model that uses an unsupervised peak recognition algorithm to identify specific features in battery charging curves,” Jayan says. “Neural network models take things a step further by learning why there might be a change in the shape of the battery’s charging curve—if a particle breaks, for example. Such a correlation between the curve shapes and various battery degradation mechanisms will be critical for prediction of both battery performance and safety in future.”
Not only is the teams’ system both interpretive and predictive, it’s also transferable to batteries made of different cathode chemistries. While lithium cobalt oxide has been the gold standard for decades, it can also be pricey. More and more, manufacturers are producing batteries made of other materials, so it makes sense to have a system that’s adaptable to them. (The model was first tested on lithium nickel oxide cathodes and was then transferred successfully to lithium cobalt oxide.) Accurately assessing battery health is also important for allaying safety concerns when dealing with emerging battery materials because their longevity and endurance haven’t been studied so extensively, but they will likely be relied upon to accommodate an increasing number of vehicles.
One of the most useful resources for the future of this research area is data taken from electric vehicle batteries that are out on the road. Using real-world figures and complex neural networks will allow battery management systems to make charge and discharge predictions with increasing accuracy, which will create a ripple effect on how electric vehicles are maintained as they become more commonplace.
Jayan and her collaborators have applied for a patent for this research, and a paper detailing this model’s capabilities was recently published in Advanced Science.
Laisuo Su, a former Ph.D. student in Jayan’s group, was a postdoctoral fellow in Arumugam Manthiram’s lab at University of Texas at Austin. Alan McGaughey, a professor of mechanical engineering at CMU, collaborated on this work along with Shuyan Zhang, who was then a Ph.D. student in the department.