Additive manufacturing in focus
Researchers introduce an experimental method to measure melt pool temperature using a single commercial color camera during additive manufacturing.
Additive manufacturing (AM) techniques are only as strong as the weakest parts they produce. Despite being regarded as a mature AM technology, laser powder bed fusion relies heavily on trial and error. To guarantee quality, researchers need to monitor parameters like the temperature of the melting powder during the build process. But how can they measure the temperature of metal powder when the melt pool moves at speeds up to one meter per second?
New research published in Additive Manufacturing, introduces an experimental method to measure melt pool temperature using a single commercial color camera. Accurate temperature measurements of the melt pool can be used to predict and identify defect signatures, such as keyholing, which can lead to cracking and porosity that can result in unsuitable parts.
“These melt pool temperature field measurement techniques and the measurements themselves are entirely unique,” said Jack Beuth, a professor of mechanical engineering.
Our methodology can be applied to any color camera to monitor and better understand melt pools that yield high-quality parts for a wide range of AM processes.
Jon Malen, Professor, Mechanical Engineering
“Our methodology can be applied to any color camera to monitor and better understand melt pools that yield high-quality parts for a wide range of additive manufacturing processes,” added Jon Malen, a professor of mechanical engineering.
To sense visible colors, the team used a commercial color camera, which has a built-in Bayer filter on the sensor with two green pixel filters for every red and blue pixel filter. Because each pixel senses light from only one color, the team acquires unique measurements for each pixel. Using a technique called demosaicing, the team reconstructs a full color image and measures the ratio between each of its colors to calculate the temperature. This novel ratiometric approach avoids complications related to surface properties and view factors that challenge the application of conventional IR imaging to AM processes.
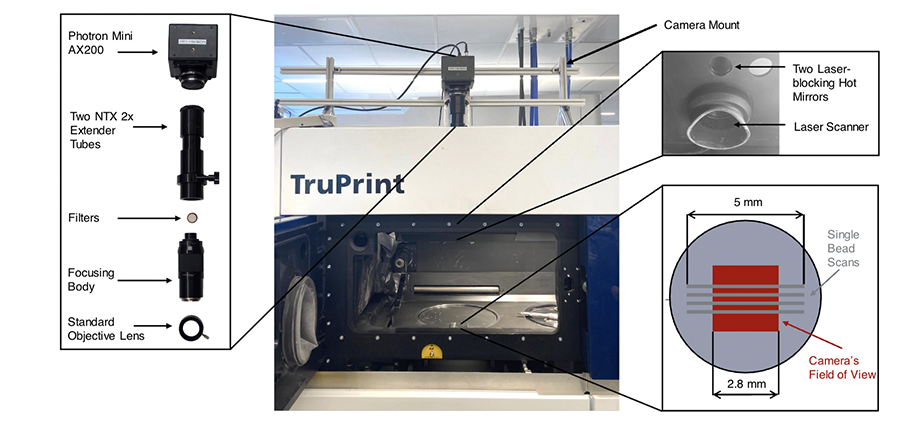
Camera mounted on laser powder bed fusion equipment enables melt pool temperature measurements.
“Without analysis, the temperatures of these liquid metals are interesting but don’t directly explain the physics in the melt pool,” explained Alex Myers, a Ph.D. candidate co-advised by Malen and Beuth. “We determined unknown parameters in a computational fluid dynamics model using the experimental results to tell us more about what happens at the microscale of the melt pool.”
Peak temperatures in the melt pool helps researchers understand material vaporization during production while the gradient toward the tail of the melt pool helps them to understand the microstructure of the final part. Understanding the physics in the melt pool is critical to ensuring quality parts because if too much of the material vaporizes or the melt pool becomes unstable, manufacturers could end up with entirely different material properties and defects that render the part unusable.
“We can look into the science of AM now and not just monitor the process,” said Guadalupe Quirarte, a Ph.D. candidate in Malen’s lab.
This is opening the door to a more complete and fundamental understanding of how process parameters affect melt pool physics, which is a central issue in AM process development.
Jack Beuth, Professor, Mechanical Engineering
Supplemental materials are available with the paper to enable researchers at any company or university to recreate this system on their own machines.
Moving forward, researchers at Carnegie Mellon plan to use this technique to understand different processes like wire arc additive manufacturing and directed energy deposition.
“These measurements and analogous simulations are opening the door to a more complete and fundamental understanding of how process parameters affect melt pool physics, which is a central issue in AM process development,” said Beuth.