Decarbonizing industry with 3D-printed stacked columns
Researchers at Carnegie Mellon University are exploring ways to reduce emissions from power plants using post-combustion carbon capture via absorption through additively manufactured stacked columns.
Carbon dioxide emissions from the combustion of fossil fuel accounted for 73% of total U.S. greenhouse gas emissions in 2020. Researchers at Carnegie Mellon University are exploring ways to reduce emissions from power plants using post-combustion carbon capture via absorption through additively manufactured stacked columns.
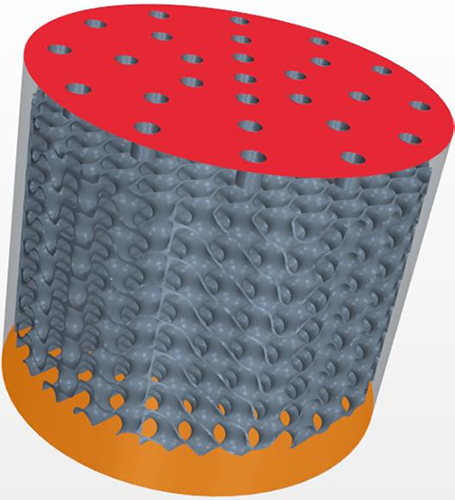
Source: College of Engineering
Three-dimensional view of the computational domain showing the Schwarz-D column.
Post-combustion capture uses predominantly chemical solvents to separate carbon dioxide out of the exhaust gas from fossil fuel combustion. Traditional packed columns—structures filled with a packing material that allows fluid to move from one end to another and enable gas to react with a higher proportion of liquid solvent—are being explored for industrial application. In order to deploy packed columns, their hydrodynamic factors need to be carefully evaluated. This is where Grigorios Panagakos, an assistant research professor of chemical engineering, comes in.
Panagakos’ research group worked through the National Energy Technology Laboratory (NETL) in partnership with the Pacific Northwest National Laboratory (PNNL) and the Lawrence Livermore National Laboratory (LLNL) to design and test the hydrodynamics of an additively manufactured column called the Schwarz-D. Under Panagakos’ lead, the PNNL team conducted 3D multiphase flow simulations to understand the hydrodynamic characteristics of the stacked column and LLNL 3D printed packings of the Schwarz-D geometry and conducted experimental studies on those structures.
The Schwarz-D is a triply periodic minimal surface (TPMS) structure that can be used simultaneously for heat and mass transfer. TPMS structures consist of two interpenetrating fluid volume domains separated by a thin wall. TPMS structures exist throughout nature (e.g. biological membranes and rock crystals) and exhibit superior structural strength using a minimum amount of material. TPMS structures also exhibit improved heat transfer and mass transfer properties due to higher specific area and excellent permeability, making them a good choice for heat and mass transfer systems.
“The major driver for any technology is the cost,” said Panagakos. “If we can optimize the column to be smaller and more efficient, we make the technology more viable for industrial use, but in order to do that we have to take into account all of the physics behind it.”
We have to take into account the physics behind it to make the technology more viable for industrial use.
Grigorios Panagakos, Assistant Research Professor, Chemical Engineering
To enable the maximum amount of CO2 to transition from gas to liquid, the group needed to monitor the interfacial area between the two phases. They extensively explored the impacts of the liquid and gas loads, solvent properties, and contact angle—a quantitative measure of wetting of a solid by a liquid—on the interfacial area and pressure drop in the Schwarz-D packed column. The simulations were also validated against experimental data gathered by the group. Furthermore, the performance of a traditional Monoethanolamine (MEA) solvent was compared to that of a state-of-the-art, water-lean solvent called EEMPA N-(2-ethoxyethyl)-3-morpholino propan-1-amine.
“We are working with our collaborators on how to take the very detailed information that we gain through our simulations and connect it on a multi-scale level modeling approach with higher level systems.”
Post combustion technology is relevant to all point sources of CO2 emission and can therefore be an essential tool in decarbonizing not only the energy sector but industries like cement, petrochemical, and steel as well. This research was the first time simulations were used to understand a two-phase system using TPMS geometries. The outcomes advance the understanding of the hydrodynamics of additively manufactured packed columns and provide insight into potential opportunities in chemical processes’ intensification in general.
The work was sponsored under the Carbon Capture Simulation for Industry Impact (CCSI2) family of projects, a flagship project on carbon management from the Department of Energy (DOE).