Measuring macro with micro
Taylor earns Air Force Young Investigator Research Program funding to develop next generation sensors with DNA and PNA.
Realizing the importance of measuring the stress heavy machinery undergoes, the United States Air Force has awarded Assistant Professor of Mechanical Engineering Rebecca Taylor with funding to develop so-called “nanosprings,” which could stick to soft materials or eventually be sprayed onto metals or other conventional materials to estimate the mechanical strain a piece of machinery endures. The nanosprings would allow mechanics and engineers to monitor the integrity and function of mechanical equipment, such as struts or aircraft components.
“It’s important with mechanical components to see what’s happening in real time,” Taylor says. “DNA nanosprings, when in soft materials or sprays, don’t require dangerous chemicals to give extremely sensitive strain readouts. Thinking of nanosprings this way gives ideas about what the next generation of sensors could be.”
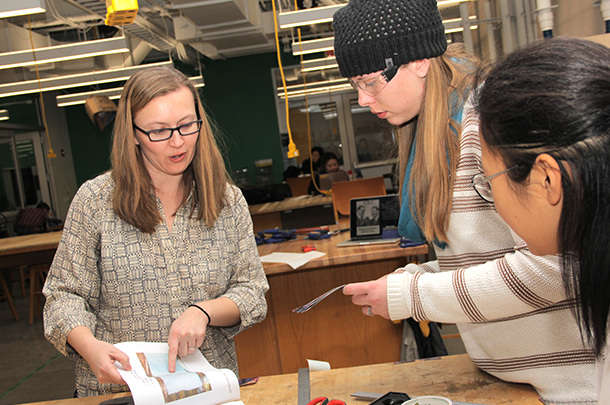
Source: Carnegie Mellon University College of Engineering
Rebecca Taylor joined CMU’s Department of Mechanical Engineering in 2016.
Taylor’s research focuses on building nanostructures to measure strain, the deformation of a material under force. These nanostructures are composed of DNA helices formed into tubular structures, which are shortened in selected regions to create a twisted, spring-like structure. The “nanosprings” are decorated with fluorescent chemicals such that, when twisted, the nanosprings emit different colors of light depending on their displacement. By then reading the relative color output, which indicates the degree of displacement, researchers can measure the deformation of the nanospring.
The new “twist” with Taylor’s research is that she has a possible method to rapidly and reversibly untwist and re-twist the nanosprings. She posits she can accomplish this using a stress relief technique with a material similar to DNA: peptide nucleic acids (PNAs). PNAs are nearly identical to DNA, but bind more strongly to DNA than DNA itself.
Taylor’s nanosprings use a mixture of PNA and DNA, and the stronger bonds between the two lend durability to the nanosprings. Reversible twisting allows the nanosprings to reliably and actively show their deformation via relative color output. When used on mechanical equipment, the nanosprings could then indicate strain.
Thinking of nanosprings this way gives ideas about what the next generation of sensors could be.
Rebecca Taylor, Assistant Professor, Mechanical Engineering, Carnegie Mellon University
Taylor’s first goal is to check the accuracy of using these nanostructures to measure strain by sticking the nanosprings to elastic films whose stretch is already known. Her second goal is to use stress-relief to twist and untwist the nanosprings to see how much spring deformation she can create just using PNA actuation. This second focus may pave the way for using nanosprings to measure material stiffness in addition to strain. Stiffness refers to a material’s resistance to deformation. Knowing the stiffness of a fuselage, for example, then informs mechanics and engineers of how much force the machine withstands before functionality is compromised.
Over the next few years, Taylor’s team expects to verify their experiments and submit their findings to the Air Force Office of Scientific Research. Funding for this project comes from the Air Force’s Office of Scientific Research Young Investigator Program.
Taylor runs the Microsystems and Mechanobiology Lab at Carnegie Mellon University. She also holds a courtesy appointment in the Department of Biomedical Engineering.