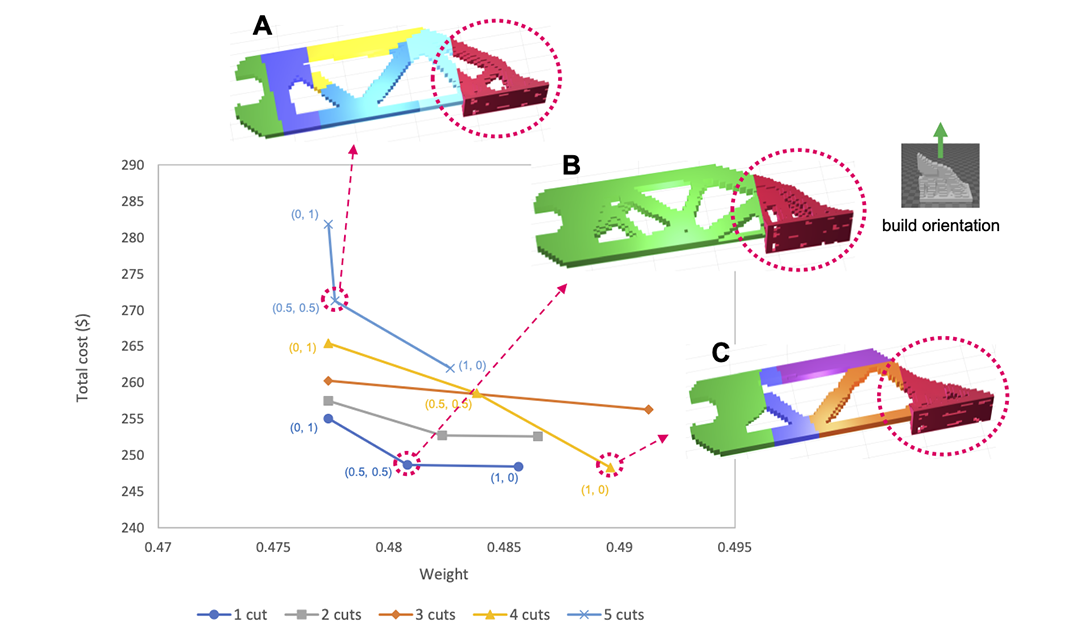
Project status: completed
This project generated an algorithm to automatically redesign the geometry and parts consolidation of a given assembly system design for metals additive manufacturing (MAM). The algorithm is a 3-D topology optimization that seeks to minimize AM production costs as well as system weight considering material inputs, printing and removal of support structures, machine costs, labor costs, and finishing steps. Test-bed results have been demonstrated on an automotive brake-pedal assembly.
The MAM topology optimization algorithm coupled with the selection of segmentation cuts within the user-provided assembly system. The algorithm provides the optimal selection of cuts including different cutting angles and locations for x, y, z axes—which reduced support structures and thereby the production costs of MAM and prevented the topology optimization from converging to an inferior solution. The method was applied to the test-bed assembly system to generate optimal placement of segmentation cuts and topology redesign of components, and optimized the number of segments as well as the placement of segmentation cuts using the tradeoffs identified between the number and size of components, and the support structures that are required during build.
Through this work, it was observed that the placement and angle of segmentation cuts significantly affect the amount of shadow volume, geometry, and production costs. Results showed that the optimization achieves a 30% lighter part than the original assembly system design. The results also showed an important tradeoff driving the optimal level of consolidation for assembly systems: consolidating additional parts serves to eliminate assembly steps, but also may increase the amount of support structures needed for larger, consolidated parts.
In summary, the optimal level of consolidation is affected by the material with higher cost and embodied-energy materials driving the optimal level of parts consolidation downward.
Pictured above: Pedal assembly optimization results (material: Ti-6Al-4V)
Next Manufacturing research area: Design