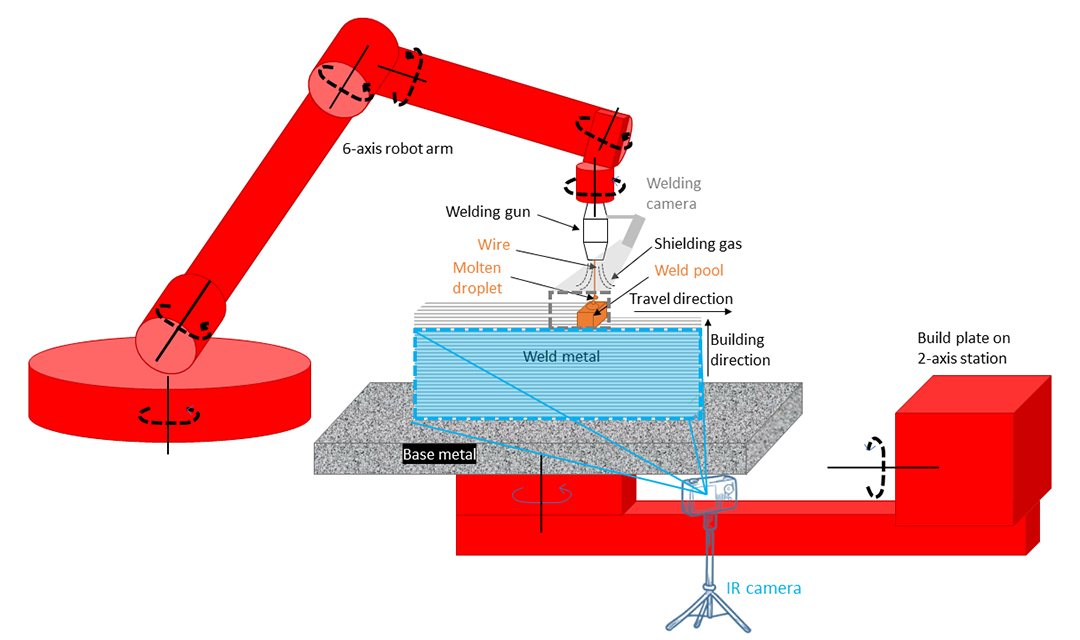
The benefits of large-scale additive manufacturing (AM) processes such as wire arc AM (WAAM) are material savings, short lead times, and cost savings. Material savings and reduced replacement by facilitating on-site repair of large, damaged parts with minimal decommissioning time also add sustainable manufacturing elements to this project. For use in real-world applications, it is required to understand the part properties governed by the material microstructure and defects.
However, for these large-scale parts, it is not practical to fabricate witness coupons in the same build to evaluate the as-fabricated material quality. At the same time, it is also impractical to perform destructive testing of a few components in batch production to assess the part performance. Hence, it is necessary to track the material microstructure and micro/mesoscale defects as the part is built.
These material outputs, in turn, depend on the weld deposition parameters and the local part geometry in each layer during the layer-by-layer fabrication. The primary objective of this effort is to integrate in-situ process monitoring at the weld pool-level and part-level with experimental process modeling and steel welding metallurgy principles to evaluate the possibilities and challenges associated with predicting the as-fabricated part microstructure in the WAAM process. The success of this project will result in a non-destructive evaluation of the material microstructure and properties and a pathway to manufacturing process optimization. This project contributes to strategic growth in large-scale manufacturing processes, automation, and repair.
Next Manufacturing research area: Materials development