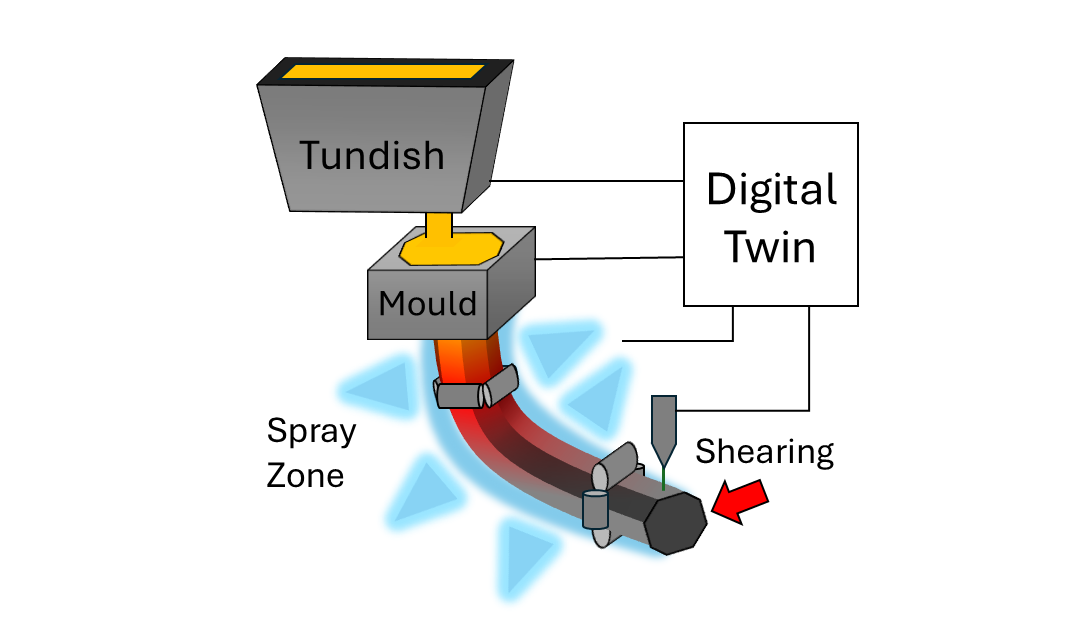
A micro mill is a small-scale, highly productive version of a steelmaking plant, with a compact combination of an electric arc furnace, continuous billet caster, in-line induction heating and uninterrupted rolling. This project develops a digital twin that accurately and rapidly mimics the steady-state and transient thermal field of the micro mill caster. Using this, researchers are able to develop a heat-transfer model that runs much faster than the actual process, resulting in a true digital twin that can interact with plant measurements in real time. Such a twin could be used in both plant operation and training of operators. The approach develops a dynamic finite-difference model of heat extraction along with training a surrogate model to reproduce the model outputs at increased speed.