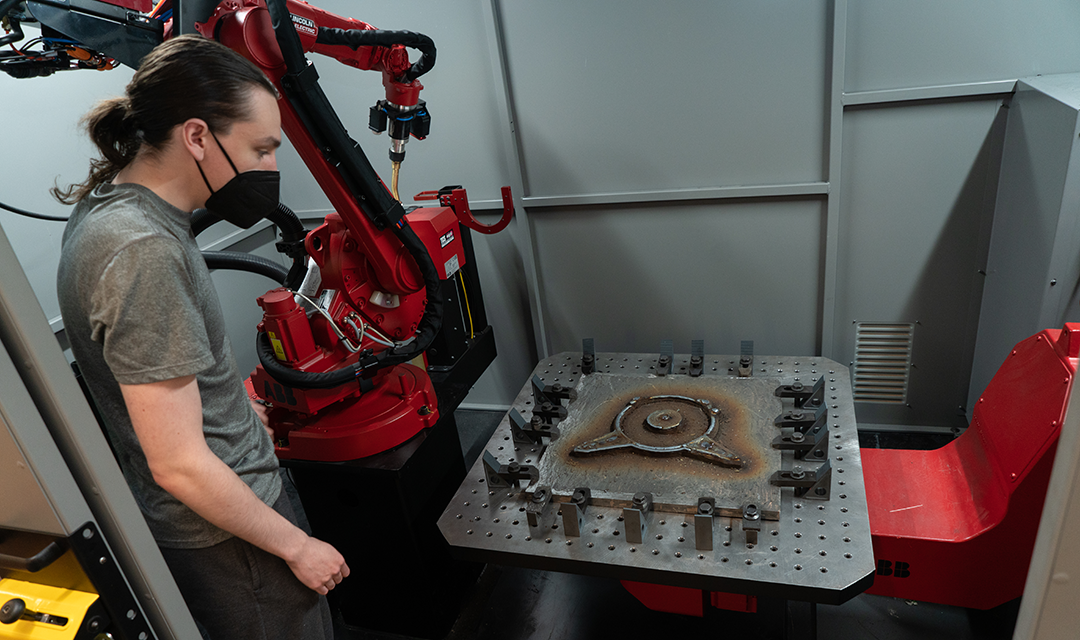
A post-process machining step to produce net-shape parts with improved tolerances is being developed to address the limitations of conventional Wire Arc Additive Manufacturing (WAAM) technology. The aim is to:
- detect and flag macro-scale defects, such as residual stress-related deformation and weld overflow that impact geometric accuracy during the production process
- provide in-situ reconstruction of the part geometry while also monitoring part quality via an online inspection tool that generates information to aid in the understanding of defect evolution during the layer-by-layer manufacturing process
An in-process robotic inspection and associated path-planning algorithm that can augment existing WAAM workflows with an intelligent process monitoring system can eliminate additional post-inspection procedures and reduce overall lead time and associated costs.
Next Manufacturing research area: Process monitoring and control
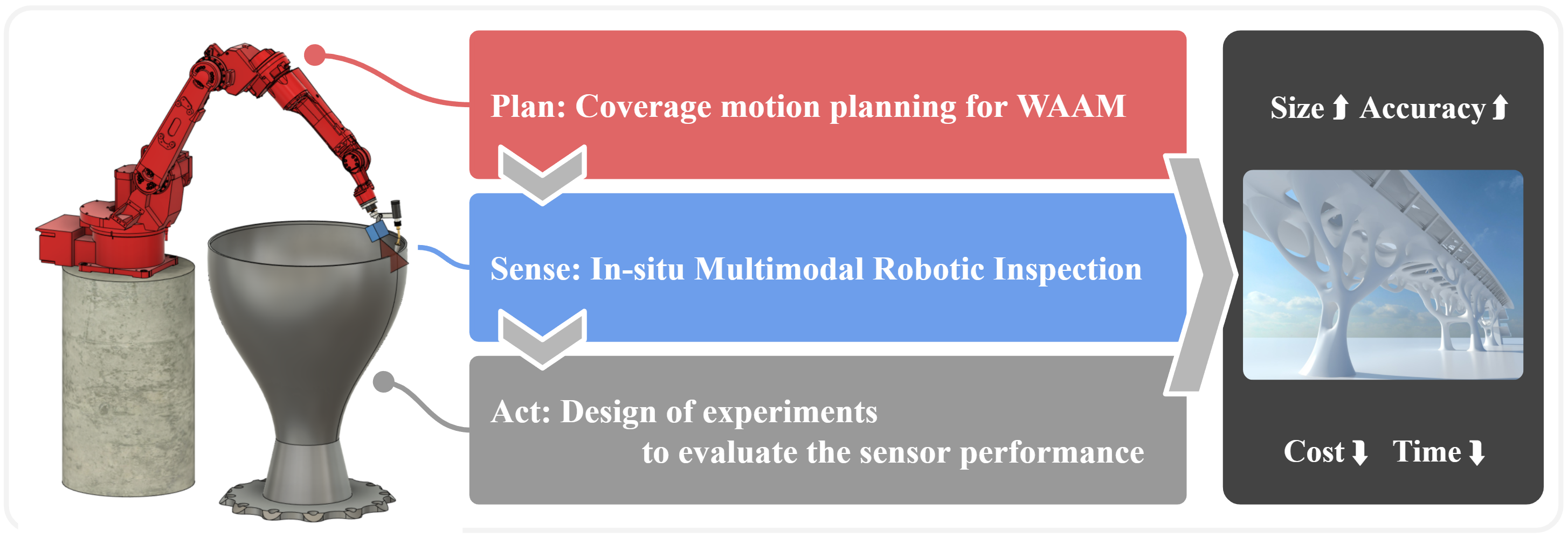
Source: Manufacturing Futures Institute
Infographics of the MFI-rWAAM project scope and potential impacts.