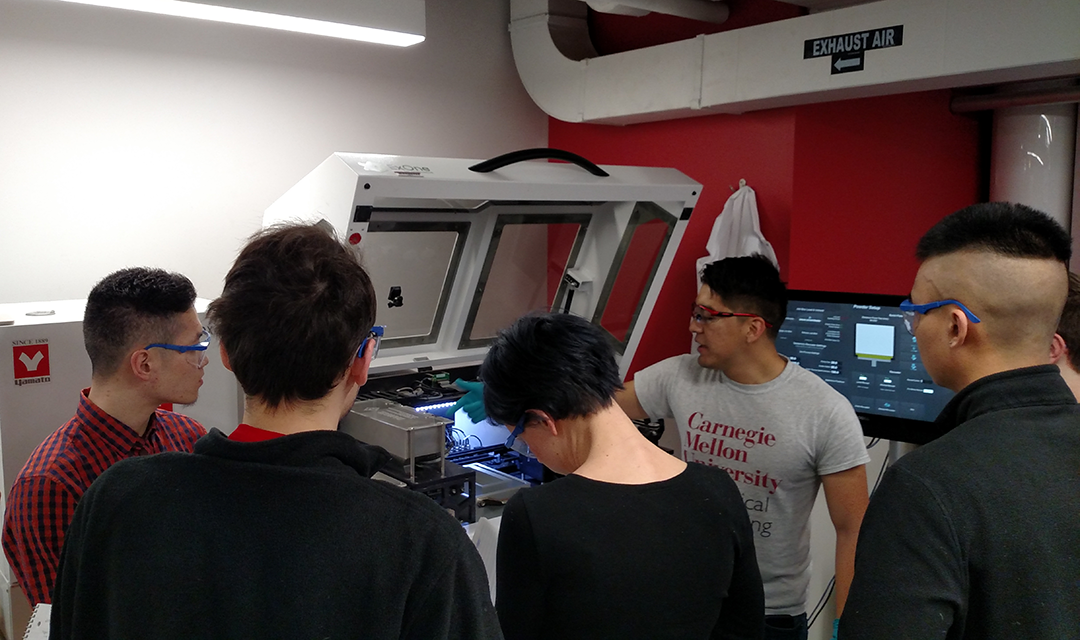
Additive manufacturing (AM) has attracted interest from both industry and academia in recent years. Understanding process-structure-property relations in AM parts has been a long-standing goal in the manufacturing and materials community. While empirical modeling requires time-consuming and expensive experimentation, physics-based modeling of material behavior involves a complete understanding of the effect of microstructure on final part property, often based on assumptions related to material failure, and requires validation. In this work, we use data-driven approaches to establish structure-property relations and understand variability in AM process. Specifically, we focus on binder jet AM of tungsten carbide-cobalt (WC-Co) composite used in cutting tools. This project establishes a collaboration between Carnegie Mellon University and Kennametal to accomplish the following objectives: (1) determine data requirements to quantify microstructure – grain size, porosity, and cobalt binder in WC-Co, (2) identify microstructural features with a strong correlation to the material property (tensile rupture strength), and (3) delineate the contribution of grain size, porosity, and cobalt binder to the strength. This work lays the foundation to understand and predict the effects of microstructure on part property. Carnegie Mellon University graduate students involved in the project will gain expertise in manufacturing, materials, and data analysis valuable to industries such as Kennametal.
Project partner: Kennametal