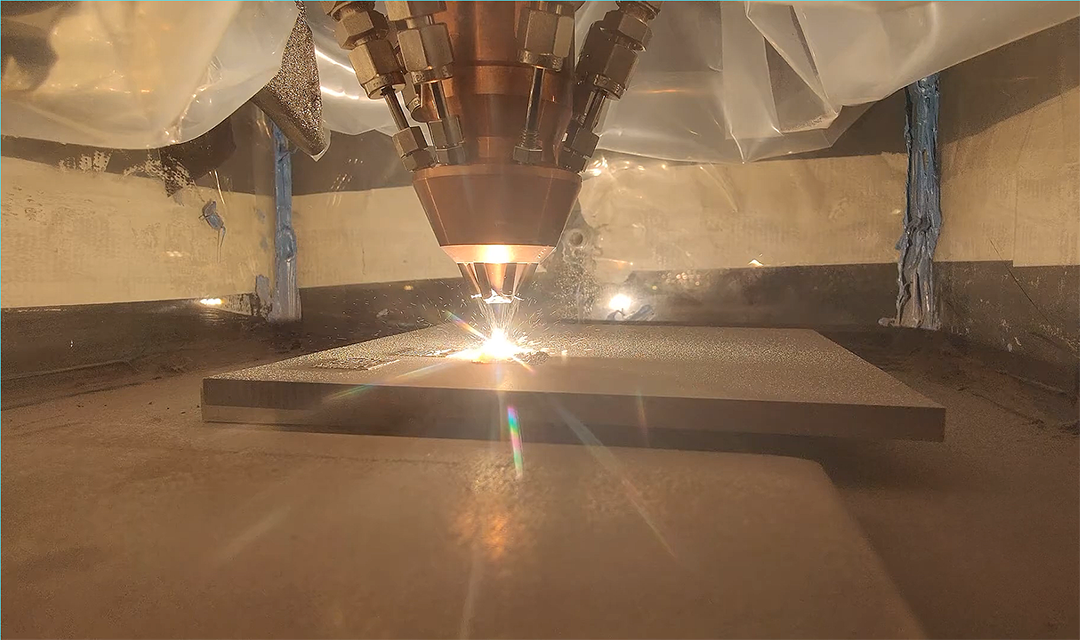
There are limited options for materials that can perform well at extremely high temperatures (above 2000°C). Alloys of refractory metals, e.g. tungsten, are candidates, but their properties at low temperatures make component fabrication and usage challenging. Additive manufacturing is a potential solution, but the process parameters needed to fabricate defect-free parts, as well as the effects of additive processing on material properties, are not fully known. Tungsten-base alloys can have high temperature properties, but porosity and cracking frequently occurs after additive manufacturing.
We will use computational thermodynamics calculations, machine-learning regression models, and heat transfer calculations to predict alloy behavior during processing and in-service. We will build test structures using additive manufacturing methods to assess and optimize the model predictions. The objective of this work is to develop a new refractory alloy with excellent properties at extremely high temperatures that can be successfully produced by additive manufacturing methods.
The goal of NASA Early Stage Innovations (ESI) is to accelerate the development of groundbreaking, high-risk/high-payoff space technologies to support the future space science and exploration needs of NASA, other government agencies, and the commercial space sector.
Project partner: Lockheed Martin