This project develops an explicit 3D isogeometric topological design software toolkit for metal (aluminum alloy) heat exchangers. Given the state-of-the-art research, topological design for 3D metal heat exchangers has been a challenge, considering complicated multi-physics equations. Using isogeometric analysis (IGA), novel numerical efforts highlight new contributions of this data-driven project to the heat exchanger design in contrast to previous studies where conventional design methods were involved based on classic finite element analysis and mathematical optimization entirely. In addition, additive manufacturing (AM) printability of the 3D heat exchanger designs is evaluated and optimized based on ML in this project. Large residual stress and deformation are prevented to guarantee good printing quality of the heat exchangers. Some practical AM processing constraints are considered in this portion of research. On the one hand, overhang features, enclosed inside voids, and sudden transitional change in the cross section are avoided for the 3D heat exchangers. A ML model based on deep neural network (DNN) is employed to implement automatic detecting and filtering for the above issues when an arbitrary geometry is given. When the aforementioned issues are detected, some manual re-design work is needed to modify the geometry of the heat exchangers to ensure robust printability and easy de-powdering of the real build. On the other hand, in order to facilitate the printing process, some specific efforts are devoted to the support structure design. At least two feasible layouts of the support structures are tested. Moreover, easy part removal is also considered for the support structure designs. The ML-based printability evaluation, enhancement methodology, and support structure design distinguish the project from existing studies of 3D heat exchangers.
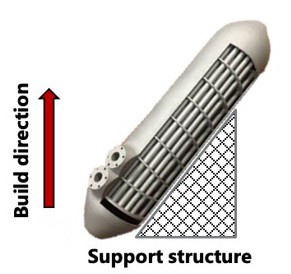