Wearable and stretchable electronic devices
Jacob Williamson-Rea
Sep 15, 2020
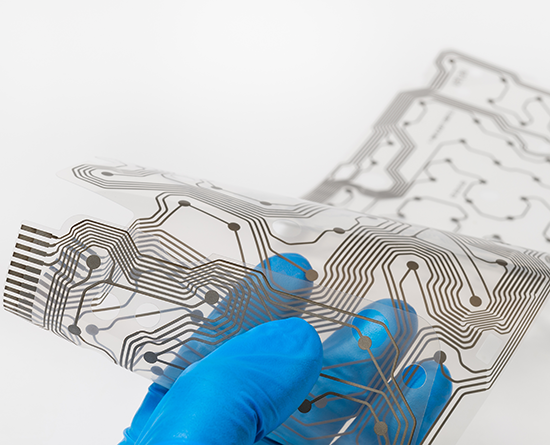
Source: Carnegie Mellon University
A group led by Carmel Majidi and Burak Ozdoganlar, professors of mechanical engineering at Carnegie Mellon University, teamed up with Liquid X, a Pittsburgh-based startup company. Liquid X manufactures metal ink technologies, and this collaboration expanded upon an existing relationship, accelerating Majidi and Ozdoganlar’s research into a commercially viable product.
“The goal was to leverage our existing relationship with Liquid X. We set out to develop scalable manufacturing methods for creating electronics that are not only flexible, but also stretchable and could be incorporated into clothing and garments, or even just directly on the skin,” Majidi says.
Majidi’s research group, the Soft Machines Lab, has generally focused on soft and stretchable electronics that are compatible with human skin. Instead of using rigid metal wiring, they’re using a metal alloy made up of indium and gallium that remains as liquid at room temperature, essentially exhibiting properties of non-toxic mercury. This liquid wiring is housed within small, microscopic channels inside a silicone rubber and is used to wire together the same transistors, microprocessors, and power regulators found on a circuit board in a smartwatch. But instead of a rigid and bulky watch, this technology is bendable, stretchable, and waterproof.
The liquid wiring allows the soft devices to stretch to over twice their natural length, making it perfect for wearable health monitoring, including measuring the user’s heart rate, blood-oxygen levels, and muscle and nervous system activity.
“We really focused on developing a scalable manufacturing process for the technology during this PITA project,” says Kadri Bugra Ozutemiz, a former team member co-supervised by Majidi and Ozdoganlar who recently completed his Ph.D. “We developed the skeleton of this fabrication flow — we figured out a way both to mass fabricate the liquid metal circuit boards and to integrate chips with these liquid metal circuit boards to make them fully functional. The circuits are stretchable and soft at the same time. They consistently work under deformation without failure.”
“We had already demonstrated these capabilities in the lab, so we knew it was possible,” Ozutemiz says. “We’re still using similar materials as we did in the lab, but the manufacturing processes and sub-process that resulted from this project have made the technology overall more scalable, commercially viable, and high throughput.”
During the course of this project, the team successfully filed a patent application for the technology’s material architecture, as well as the processing and manufacturing of liquid metal. “We were very careful to work with techniques that didn’t just work in the lab under controlled conditions; we wanted this process to work in more of a factory setting,” Majidi says. Along with wearable health monitoring, the numerous future applications could include motion capture technology, too, replacing bulky data gloves and sensor suits.